Reducing CO2 Emissions with Tracegrow's Circular Approach
Lowering CO2 Emissions in Trace Element Manufacturing
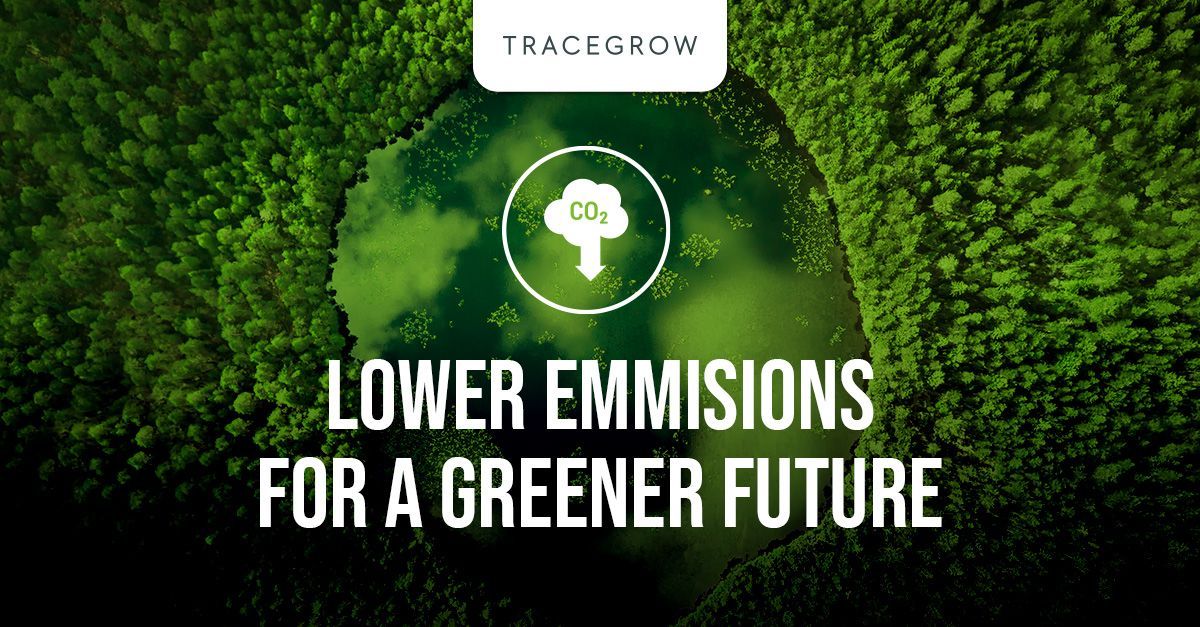
At Tracegrow, we are committed to developing sustainable and environmentally responsible manufacturing processes. Our focus is on reducing carbon emissions and minimizing the environmental impact of our operations.
The environmental impact of mining
Extracting raw materials like trace elements through conventional mining methods can contribute significantly to greenhouse gas emissions. While the industry has made strides towards adopting more sustainable practices, processes such as drilling, excavation, and ore transportation still involve substantial energy consumption, often from fossil fuel sources. Additionally, the long-distance transportation of raw materials from mining sites to processing facilities adds to the overall emissions footprint.
Recycling trace elements: a 50% emission reduction
Tracegrow has pioneered a circular economy model that addresses these emission challenges. By recycling already mined trace elements like zinc and manganese, we have achieved a 50% reduction in CO2 emissions compared to conventional mining methods for obtaining these trace elements.
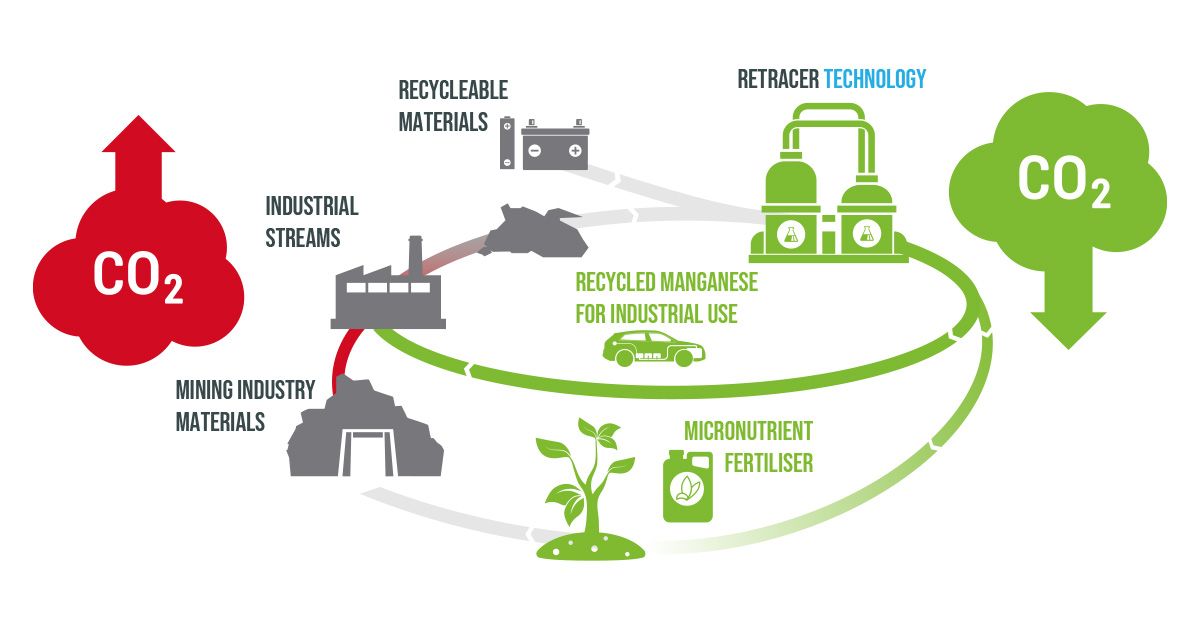
The key factors enabling this significant emission reduction are:
Eliminating energy-intensive extraction processes:
Our recycling approach bypasses the need for the energy-intensive processes involved in mining, such as drilling, blasting, and hauling of ore. This helps avoid the emissions typically generated by these activities.
Minimizing transportation emissions:
By sourcing recycled materials locally from industrial side streams, we significantly reduce transportation requirements and associated emissions. Unlike traditional mining operations, where raw materials often travel long distances from remote sites to processing facilities, our local sourcing strategy minimizes transportation-related emissions.
Energy-efficient production technology:
Tracegrow's patented RETRACER technology is designed to be highly energy-efficient, optimizing the processes involved in recovering and processing trace elements from recycled materials. This energy efficiency translates into lower energy consumption and, consequently, much lower CO2 emissions associated with the production processes compared to conventional mining and processing methods.
Second-generation RETRACER process
We are continuously striving to improve our environmental performance and sustainable manufacturing. Our upcoming second-generation process aims to set even higher benchmarks for emissions reduction in the production of trace elements. By incorporating the latest technological advancements and optimizing our processes further, we are committed to achieving even greater reductions in our carbon footprint.
Minimizing emissions through EU sourcing and manufacturing
A key driver of Tracegrow's reduced emissions is our sourcing and manufacturing operations being entirely based within the European Union. By locally sourcing recycled materials from industrial side streams and producing our trace elements at EU facilities, we minimize the carbon footprint associated with transporting raw materials over long distances. This local sourcing and production strategy allows us to significantly reduce emissions compared to global supply chains that require extensive shipping of materials from remote locations. While our finished products are distributed worldwide, keeping the sourcing and manufacturing phases within the EU enables us to maintain a low-emission footprint for those upstream processes.